Domestic petroleum, chemical and other energy industries need a large number of low-temperature steel to design and produce various manufacturing and storage equipment such as liquefied petroleum gas, liquid ammonia, liquid oxygen and liquid nitrogen.
According to China's 12th Five Year Plan, the development of petrochemical energy will be optimized and the development of oil and gas resources will be accelerated in the next five years. This will provide a broad market and development opportunity for the energy manufacturing and storage equipment production industry under low temperature service conditions, and will also promote the development of Q355D low temperature resistant rectangular tube materials. As low-temperature pipes require products to have not only high strength but also high and low temperature toughness, low-temperature pipes require higher purity of steel, and with the ring ratio of temperature, the purity of steel is also higher. Q355E ultra-low temperature square tube is developed and designed. The billet steel can be directly used as seamless steel pipe for Conveying structure. The manufacturing process includes the following three points:
(1) Electric arc furnace smelting: scrap steel and pig iron are used as raw materials, among which scrap steel accounts for 60-40% and pig iron accounts for 30-40%. Taking advantage of the advantages of high alkalinity, low temperature and high iron oxide of the ultra-high power grade electric arc furnace, the intense stirring of oxygen decarburization by the bundle oxygen gun on the furnace wall, and smelting the initial steel-making water with the high impedance and ultra-high power grade electric arc furnace, the harmful elements phosphorus, hydrogen, nitrogen and non-metallic inclusions in the molten steel can be effectively removed. End point carbon of molten steel in electric arc furnace < 0.02%, phosphorus < 0.002%; Deep deoxidation of molten steel is carried out in the process of electric furnace tapping, and A1 ball and carbasil are added to carry out pre deoxidation.
The aluminum content in the molten steel is controlled at 0.09 ~ 1.4%, so that the Al203 inclusions formed in the initial molten steel have sufficient floating time, while the aluminum content of the tube billet steel after LF refining, VD vacuum treatment and continuous casting reaches 0.020 ~ 0.040%, which avoids the addition of Al203 formed by aluminum oxidation in the LF refining process. The nickel plate accounting for 25 ~ 30% of the total alloy is added to the ladle for alloying; In case the carbon content is greater than 0.02%, the carbon content of ultra-low temperature steel can not meet the demand of 0.05 ~ 0.08%. However, in order to reduce the oxidation of molten steel, it is necessary to control the oxygen blowing intensity of the furnace wall cluster oxygen gun to control the carbon content of molten steel below 0.02%; When the phosphorus content is equal to 0.002%, the phosphorus content of the product will reach more than 0.006%, which will increase the harmful element phosphorus content and affect the low-temperature toughness of the steel due to the dephosphorization of the phosphorus containing slag from the electric furnace tapping and the addition of ferroalloy during LF refining. The tapping temperature of the electric arc furnace is 1650 ~ 1670 ℃, and the eccentric bottom tapping (EBT) is used to prevent the oxide slag from entering the LF refining furnace.
(2) After LF refining, the wire feeder feeds 0.20 ~ 0.25kg/t pure CA wire of steel to denature the impurities and make the inclusions in the molten steel become spherical. After Ca treatment, the molten steel is blown with argon at the bottom of the ladle for more than 18 minutes. The strength of argon blowing can make the molten steel not exposed, so that the spherical inclusions in the molten steel have sufficient floating time, improve the purity of steel, and reduce the impact of spherical inclusions on low-temperature impact toughness. The feeding amount of pure CA wire is less than 0.20kg/t steel, the inclusions cannot be completely denatured, and the feeding amount of Ca wire is more than 0.25kg/t steel, which generally increases the cost. In addition, when the feeding amount of Ca line is large, the molten steel boils violently, and the fluctuation of the molten steel level causes the molten steel to be sucked in and secondary oxidation occurs.
(3) VD vacuum treatment: send lf refined molten steel to VD station for vacuum treatment, keep the vacuum below 65pa for more than 20 minutes until the slag stops foaming, open the vacuum cover, and blow argon at the bottom of the ladle for static blowing of molten steel.
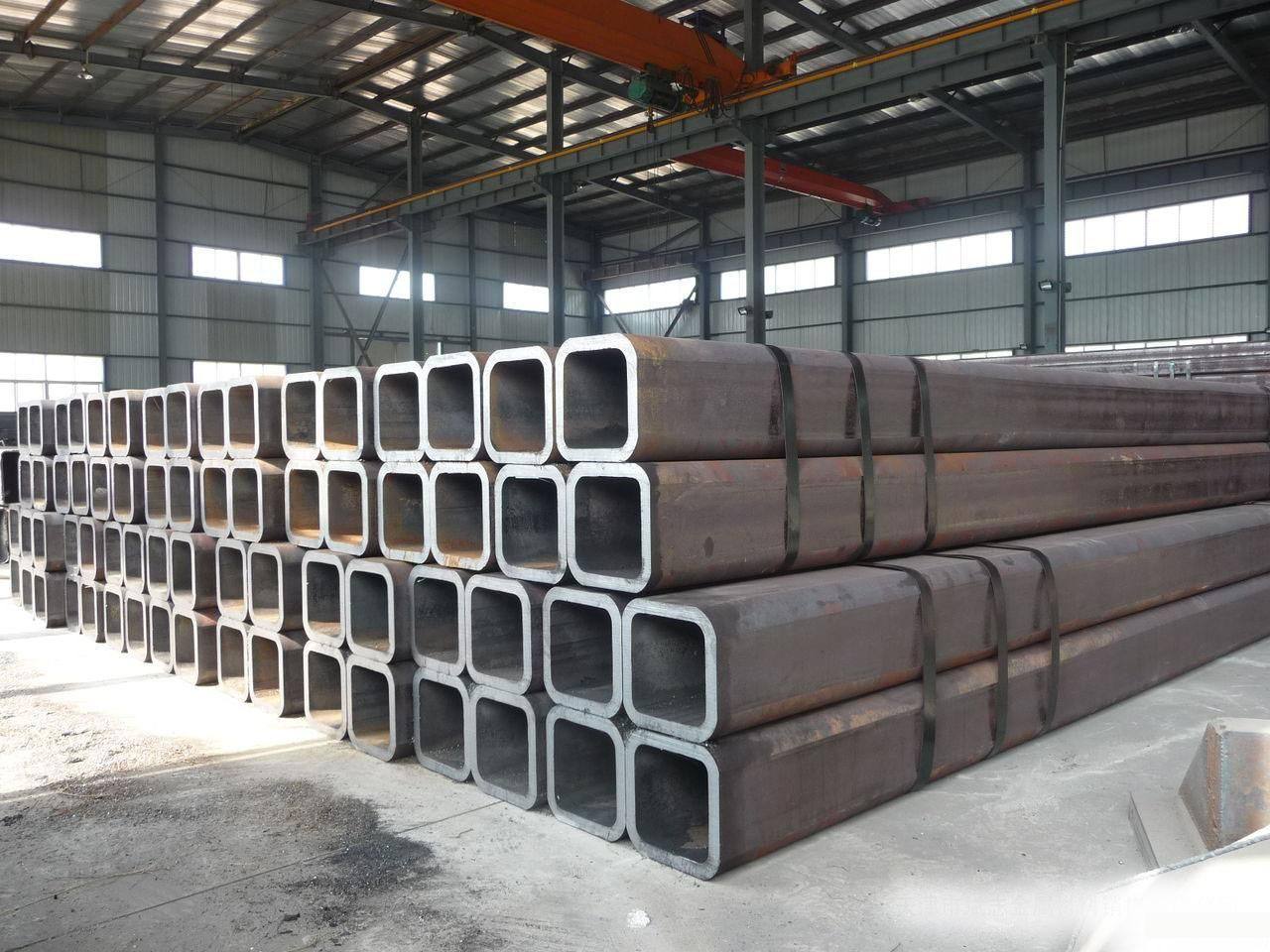
Post time: Sep-02-2022